NOUS RECRUTONS! RENDEZ VOUS SUR CETTE PAGE POUR EN SAVOIR PLUS.
Packaging Europe – Could this innovative technology replace plastic coatings and PFAS?
6/24/20224 min lire

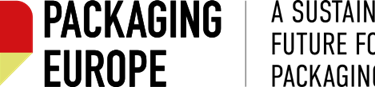
Link to the original article on Packaging Europe.
Cellulotech, a Canadian materials science company, claims to have developed a food contact-approved process that makes paper products resistant to water, grease, oxygen, and vapour – all while having no effect on recycling and composability. To learn more about this potential alternative to plastic coatings, waxes and PFAS, we spoke with the company’s founder and CEO, Romain Metivet.
Could you introduce your innovation to us?
Chromatogeny is a green chemistry reaction that grafts long-chain fatty acids on different substrates such as paper, starch, PVOH, minerals, etcetera to make them superhydrophobic while preserving their repulpability and compostability properties.
Besides the strong and lasting barriers and its environmental advantages, the process is extremely cost-competitive. We use as little as 2mg of a reagent per square meter of specific surface area. 20mg are then needed for a substrate with 10 square meters of specific surface area per geometric square meter. One kilogram of such reagent costs less than €10, so the input cost per square meter ends up being less than 0.02 cents. It’s difficult to find anything more competitive.
What’s important to understand is that it is very different from a coating – it is a chemical reaction. We are not adding a layer of a distinct material upon the surface of a substrate, but we generate permanent ester bonds onto its whole specific surface area. Chromatogeny-treated products are monomaterials, not composites and as such, they cannot be altered by plying or cutting.
Contact angles are well above the 90° mark (in some cases, they may even reach 180°) which completely inhibits any capillary uptake. These ester bonds are basically permanent, and paper that was treated two decades ago still shows the same properties today as then.
Chromatogeny not only has the potential to solve a lot of issues faced by the packaging industry in terms of costs and sustainability, but also to expand the use of paper for other industries. Our planet is a giant cellulose bio factory, and our core belief is that we have to use it as much as possible in our economy.
What’s the story behind the invention and commercialization of the solution?
More than a hundred years ago, it was discovered that paper could be made hydrophobic using long-chain fatty acids. However, this process involved a solvent, complicated conditions, and was taking days.
Twenty-five years ago, Daniel Samain, now Cellulotech’s chief scientist, discovered a new solvent-free green chemistry process that was able to do this much faster and named it chromatogeny. Since then, the environmental and barrier properties of this technology have been well studied and even published in peer-reviewed journals. However, it was maybe too early, and the first pilot that was developed more than a decade ago came short in terms of speed and efficiency which, in our opinion, has limited the adoption of this technology, until now.
Two years ago, Cellulotech was founded to start from a blank page and develop a scalable process. Instead of taking a traditional paper or printing engineering approach, we took a chemical engineering one. The new process we have developed brings the reaction time from a few seconds to just 0.1 seconds. As our grafting yield also increases, we can use fewer amounts of reagent and solve other issues that have been encountered in the past. Moreover, we are not limited by a roll-to-roll approach and can also treat whole corrugated cardboard sheets and some 3D shapes.
We have patented this new process and intend to license it as well as produce some materials for niche applications. We are now finalizing our industrial pilot plans with several partners in order to demonstrate the scalability of this solution.
Broadly speaking, what are the key applications for Cellulotech, and what separates it from conventional alternatives?
Applications are extremely diverse since this chemistry can offer a large range of barriers and strengths which offers us the ability to optimize the performance/cost ratio. In fact, we are discovering new applications quite often. I’ll mention the main ones we are focusing on as of now.
In food packaging, grafted PVOH could replace PE coatings in single-use food packaging such as paper cups, as well as eliminate PFAS. It is already approved for food contact in some jurisdictions.
For non-food packaging, as we see a large demand for a “paperization”, grafted paper offers great lasting properties that could help shift from plastic wraps such as the ones we see for paper towels or toilet paper for example or be used for all sort of e-commerce plastic-free packaging. Grafted cardboard for frozen foods is also a great potential market for us.
The ability to make corrugated cardboard superhydrophobic is also extremely interesting since it could help save some pulp but also get rid of things like paraffin for demanding applications. It also opens a new world of possibilities for this great material in construction or manufacturing. There is also potential for labels, since grafted PVOH can be used as a repulpable release paper.
Broadly speaking, chromatogeny has also the potential to get rid of the “creeping” phenomenon during storage that wastes enormous quantities of packaging and goods every year.
Beyond packaging, since grafted paper behaves like a “gore-tex”, we have shown it can be used to make 100% paper face masks or offer selective oil absorption for oil spill removal for example. We also investigate applications with textile and wood. It’s a whole new world of bioproducts that is opening in front of us and that is very exciting.
Let’s talk about end of life – does the material affect the recyclability of the materials it is applied to? Would a paper pack with the coating still be recyclable within existing paper waste streams?
Because of the process and the tiny amount of reagent used, any substrate that is initially repulpable and compostable will remain repulpable and compostable post-grafting in the existing waste streams. Moreover, the grafted molecules are fatty acid esters, something completely natural that we find all around us that is completely harmless to the environment.
What does the future hold for Cellulotech?
As of now, our goal is to finalize our partnerships and the financing of our pilot. While it is being built, we will keep working on product development projects with different corporate and academic partners and keep developing our intellectual property portfolio, especially regarding new substrates and applications.
Once the pilot is ready and running at 500 meters per minute or more, scalability will be demonstrated and we will be able to start producing niche bioproducts, run larger tests and start licensing this technology. We expect our machines to be commercially available within two to three years.
810 HUMBOLDT STREET (SUITE #A02) VICTORIA, BC, V8V 5B1 CANADA | +1 (902) 905 3076
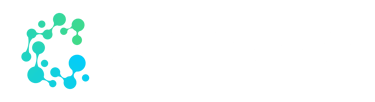
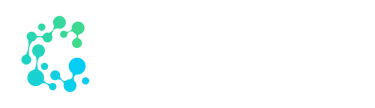